A large part of the face masks delivered to Belgium did not meet the safety norms. The filters of the KN95-masks give sufficients protection, but do not fit well on the nose bridge. A 3D printed brace offers a solution. The prototypes, inspired by Mark Fuller's concept, were tested in close cooperation with the Shortage Taskforce of the federal government and the prevention advisors of some 10 Belgian hospitals, coordinated by Herman Devriese, head of the prevention and environment department in UZ Leuven.
Reusable
The 3D-printed brace is attached to an existing mask and follows the outlines of the face. This will help the mask to fit better. Tests performed by the prevention service IDEWE show that the modified masks more than meet the safety requirements in the ATP protocol.
The braces can easily be disinfected in the hospital ensuring that, in combination with a new filter, they can be used more than once. Hospitals, care centres and private individuals that have these rejected face masks, can order the brace online. The brace is available in four different sizes.
Safe and comfortable
“Thanks to a close collaboration between the government, Materialise and UZ Leuven we have been able to create a safe solution for the rejected face masks in a short time-span", according to Herman Devriese, head of the prevention and environment department in UZ Leuven. “Thanks to the braces, the masks are safe and comply with the demand for more ease of use and comfort. For care workers that have to work a mask for hours on end, that is a necessity.” In the meantime, the first braces are already in use in a number of Belgian hospitals, including UZ Leuven.
“This is another example of a successful collaboration between Belgian innovation and our healthcare system", accordint to Minister Philippe De Backer. "I am very pleased that we are able to improve the supply for our care workers even more, thanks to all the good work of Materialise and the cooperating hospitals.”
"3D-printing allows the development of innovative solutions that can quickly be deployed worldwide", according to Fried Vancraen, CEO of Materialise. “Thanks to the flexible productions process we can quicky have prototypes to print and test. We'll be scaling the production to thousands of braces a day to help as many care workers as we can. For tens of years, Materialise has got experience in certified 3D printing in the healthcare sector, ensuring we can bring 3D-printed solutions to market quickly as well as safely".
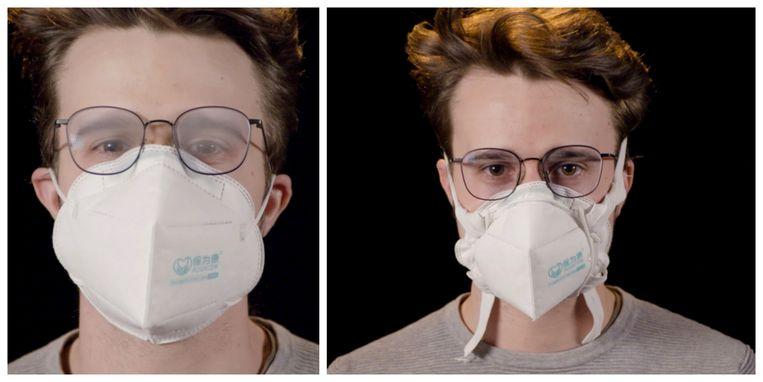
© Materialise